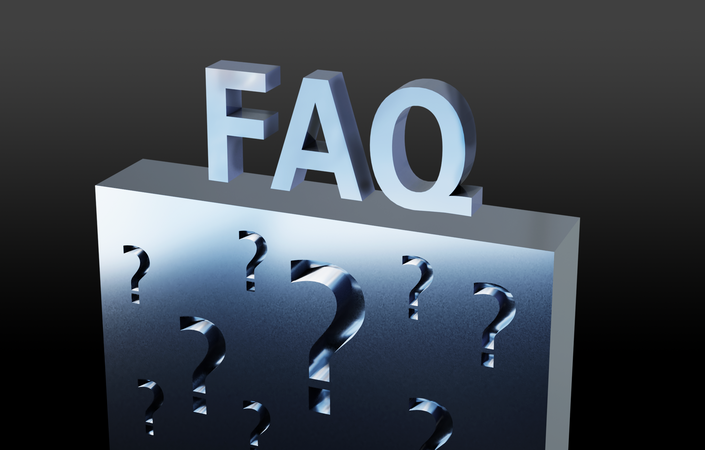
Frequently asked questions at our HEIDENHAIN Service department
Please select your topic and question. If you can't find what you're looking for, please contact our Helpline.
Search for answers
General
How do I find my nearest representative?
You can find your nearest representative here on the HEIDENHAIN website. Select your country on the world map. For the nearest HEIDENHAIN agency in Germany, simply enter your postal code.
What can I do if I forget my Filebase password?
Where can I find the mounting instructions?
You can find information about our products, including mounting instructions, in “HIF” (for customers with access information) or at our Infobase. Please send any further questions to hesis-web@heidenhain.de.
What is a DAkkS calibration?
How do I find out how old my device is?
With your serial number on hand, please contact the HEIDENHAIN Service department:
+49 8669 31-3121, service.order@heidenhain.de
Or contact your nearest representative:
Where can I send in my device for repairs?
How do I find out the cost of repairing my HEIDENHAIN device?
Contact the HEIDENHAIN Service department:
+49 8669 31-3121, service.order@heidenhain.de
Or contact your nearest representative:
Where can I see whether my device is a serial product or whether it has been moved to the Service department?
Contact our HEIDENHAIN Service department: +49 8669 31-3121, service.order@heidenhain.de
Where can I get information about the cause of failure of my repaired device?
You can request a inspection report from the relevant customer service representative:
+49 8669 31-3121, service.order@heidenhain.de
Or contact your nearest representative:
How long will it take for my device to be repaired?
Please contact the HEIDENHAIN Service department:
+49 8669 31-3121, service.order@heidenhain.de
Or contact your nearest representative:
Where should I send my defective device for a HEIDENHAIN exchange replacement?
For the HEIDENHAIN exchange service, please always send your defective devices to the address at which you requested the exchange. You can find your HEIDENHAIN regional agency here.
Traunreut campus shipping address for defective devices as part of the exchange service:
DR. JOHANNES HEIDENHAIN GmbH
Einsteinstraße 3
83301 Traunreut, Germany
What should I do if the labels from the HEIDENHAIN exchange service were not included in delivery?
What are the shipping carriers used by HEIDENHAIN?
Can HEIDENHAIN use a courier service for my replacement order, including abroad?
A courier service is possible within Germany and, to a limited extent, abroad.
Contact the HEIDENHAIN Service department:
+49 8669 31-3121, service.order@heidenhain.de
Can I pick up my device at HEIDENHAIN myself?
Can I bring in my device for repairs and wait until it is finished?
It is generally possible to wait for a repair at the Traunreut campus and regional agencies. Please first get in touch to schedule an appointment and to check availability of the replacement part.
Contact the HEIDENHAIN Service department
+49 8669 31-3121, service.order@heidenhain.de
Or find and contact your local representative.
How do I find out if my control is still being repaired?
For questions about repairs being made to your control, please contact the HEIDENHAIN Service department:
+49 8669 31-3121, service.order@heidenhain.de
Or contact your nearest HEIDENHAIN agency:
What is the warranty on my HEIDENHAIN device?
Our customers have a contractual, 12-month guarantee on serial devices. In addition, HEIDENHAIN provides a 24-month performance warranty. The total performance warranty period for new serial devices is therefore 36 months.
Devices for servicing purposes
A 12-month performance warranty applies to replacement parts.
Replacement devices
A 12-month performance warranty applies to devices from our Service Exchange inventory.
Repairs
After the repair, you receive a 12-month performance warranty on both the repaired part and the entire device.
How can I extend the warranty period?
In addition to an extended warranty (24 months), HEIDENHAIN also offers service agreements that increase the cost-efficiency of your investment and make repair costs plannable. We offer the following:
- Extension of the warranty period
- Stock-keeping
Please get in touch with your contact person in the Sales department.
Where can I find the statutory guarantee and warranty periods for my HEIDENHAIN devices?
Contact the HEIDENHAIN Service department:
+49 8669 31-3121, service.order@heidenhain.de
Or contact your nearest representative:
Where can I find the documentation for my control?
- The User's Manuals for NC programmers/machine operators can be found under Documentation in the download area.
- The Technical Manuals and Service Manuals for current controls (iTNC 530 and NCK controls) are in the HEIDENHAIN Filebase for authorized customers.
- The Technical Manuals and various service documents of older controls are available to everyone for download under Documentation.
How can I back up data on my control?
Different methods are possible depending on the type of control. These possibilities are described in detail in the respective User’s Manual.
Tip: search for “data backup” in the PDF document.
How do I establish a connection to my control?
The easiest way to establish a connection to the TNC from a directly connected PC is with TNCremo/TNCserver.
If the TNC control already has a network card (iTNC 530 or higher), then at least one IP address must be provided. Please refer to the description in the User’s Manual, because the procedure varies slightly based on the NC software.
All of the TNC controls also feature an RS-232 interface (Recommended Standard 232). But due to its very limited capabilities and speed, this interface should be used only on older models.
How can I integrate my control into my corporate network?
How can I connect a network share to my control?
Depending on the type of network share and version, it can be made visible as a drive on the TNC. Because this process varies slightly based on the NC software, please refer to the User's Manual.
My control is old, but it still works. Does HEIDENHAIN offer an upgrade to a current control?
HEIDENHAIN does not offer an upgrade to a current control. We recommend contacting your machine manufacturer or an experienced specialist who performs “retrofitting”.
We'd be happy to recommend experienced companies. Contact us.
How can I check the control's statuses and run times?
Where can I obtain end-user support for implementing new functions on my machine (e.g., for the PLC)?
We recommend contacting your machine manufacturer or a qualified retrofitter.
We can happily recommend experienced companies. Contact us.
What do the abbreviations AVD, CTC, ACC, PAC, MAC, and LAC stand for?
AVD: Active Vibration Damping
CTC: Cross Talk Compensation
ACC: Active Chatter Control
PAC: Position Adaptive Control
MAC: Motion Adaptive Control
LAC: Load Adaptive Control
For detailed descriptions, visit these links:
https://www.klartext-portal.com/en/tips/functions/dynamic-precision/
https://www.klartext-portal.com/en/tips/functions/dynamic-efficiency/
How can I create a log?
For the purpose of error diagnosis, all error messages and keystrokes are documented in a log.
A log can be created on the control via the “LOGBOOK” code number or via the ERR button → LOG FILES soft key → LOG on more current controls.
There is also the possibility of creating a log from an external PC via TNCremo: go the "Extras" menu and select "Receive log".
How can a copy of the data carrier of a HEIDENHAIN CNC control be created using the HEIDENHAIN Clone external hard disk drive?
The Infobase provides you with full information about our products.
Search the User’s Manual for the respective ID or “Clone”.
Where can I find information about the error messages on the machine?
You can find the information in the machine manual from the machine manufacturer. Press the “ERR” and then the “HELP” key. To find more information about PLC messages in the machine manual and about NC messages, visit the following link:
http://content.heidenhain.de/doku/tnc_guide/html/en/index/1242135142456/1242135142456.html
What information do I need to provide in my e-mail in order for the Service department to provide fast help for controls?
Your e-mail should ideally contain the following information:
- Ticket number (if known)
- Your corporate address
- Person of contact (if a phone call has taken place)
- Precise description of the error
- Servicing file (created directly after the error occurred)
- The control model
- The machine manufacturer
If needed, feel free to use our contact form.
What remote maintenance options does HEIDENHAIN offer?
There are several possibilities depending on what is needed:
- TNCremo PLUS -
This allows you to display a live image of your control.
For more information, please refer to the following link:
https://www.heidenhain.com/products/digital-shop-floor/connected-machining
- TeleService -
This lets you display a live image of your control and operate it.
- StateMonitor -
This gives you fundamental information about machine availability, whether a program is running, or whether an error is shown. For more information, please refer to the following link:
https://www.klartext-portal.com/en/software/machine-data-collection/
- SRI State Reporting Interface -
With its State Reporting Interface (SRI) software option, HEIDENHAIN offers an interface for easily making machine operating statuses available to a higher-level MES or ERP system.
In order to avoid data loss, does the control need to keep running while the buffer battery is being changed?
Newer controls (TNC 4xx or later) feature a GoldCap capacitor, which ensures that the data are buffered while the battery is being changed. However, the battery should not be removed for an extended period of time. Older controls do not have a capacitor, and their data are not saved when the control is switched off.
Is it possible to view the states of the inputs/outputs on the control?
My tool changer does not work anymore. How can I retract it?
The remote connection to the control is not working. What can I do about it?
I want to install an indexing head on my machine. Does this work with my HEIDENHAIN control?
Who can help me with questions regarding the MillPlus?
How can I create a log file?
How can I correctly evaluate the temperature on the control if a replacement motor is installed with a KTY84-130 temperature sensor instead of a PT1000?
In software version 606420-04 SP12, we introduced machine parameter MP2207.x (overwrite “Type of temperature sensor” from motor table). This machine parameter can be modified as follows:
* = Entry in the motor table is active
0 = KTY84-130
1 = PT1000
In NC software 606420-04 SP5 or later, the motor table contains the entry “TEMP_SENS”. You can change this entry with a PLC authorization.
For older controls, we offer the PT1000-KTY converter (ID: 1219990-02).
When the tool length appears in the tool table via touch-off, the difference relative to L from TOOL.T is no longer used. Instead, the value is taken directly from the ACTL display.
The behavior of the “actual position capture” key was intentionally changed for the introduction of NC software 340590-10. The value is now always taken from the value of the programmed tool axis as shown in the position display. To receive the correct value, perform the following steps:
1. Enter L=0 and DL=0 for the tool, and move the tool to the touch-off surface.
2. Press the “actual position capture” key.
The displayed value is always transferred to the table without undergoing any calculations. This process also takes the programmed tool axis into account rather than merely “Z”.
Where can I find the current version of my software (HEIDENHAIN DNC/TNCremo/etc.)?
What is the highest software version that my (old) control can run with?
Who can enable my software option?
Where can I find the NC software version of my machine?
I would like to install the latest NC software on my control. What do I need to do?
Which ports do I need to enable for StateMonitor?
How do I activate enhanced DNC Logging in Windows?
- Start the “Create HeidenhainDNC connections” program, located in %PROGRAMFILES(x86)%\HEIDENHAIN\SDK\Connections.
- After pressing the “DNC Logging” button, the HEIDENHAIN DNC Logging Features dialog box appears.
- Only the “Main objects / Basic” option is set as a default. After selecting all options, you can re-close the dialog box by pressing the “OK” button.
- Restart your application in order for the changes to take effect.
Does my machine have option 18?
Can I run an old programming station on a current version of Windows?
This cannot be answered across the board and sometimes depends on other factors such as a graphics driver. To find out the operating systems for which the individual versions are released, see the information in the download area.
It is sometimes possible to adapt a current and therefore runnable programming station to the cycle structure of an older version, thus allowing programming errors to be reduced.
As a last option, a Windows XP computer, for example, can be used in a virtual environment in order to install the old programming station.
How can I download programs to and from the programming station?
How can I obtain the machine manufacturer functions on my programming station?
Why is my programming station not recognized as a full version?
The software of the test version and full version is identical. It is enabled via a hardware dongle that is ordinarily built into the programming station keyboard. Whether this kind of dongle or an external dongle is connected depends on the given driver. The driver can be downloaded from our website free of charge but is dependent on the model. If you are unsure, then simply install both drivers.
If the dongle is displayed correctly in the Windows device manager and is still not recognized by the software, then this may be due to the following:
- Incorrect software version; dongle license does not match
- VirtualBox does not use the dongle properly → Check installation
- Multiple programming station are running (the first one becomes the full version)
The VirtualBox programming station does not start after the installation. What can I do?
- Download the most recent version of the VirtualBox programming station of the TNC 640 from the download area in order to ensure that the installation file is up to date.
- Open the downloaded .zip file with a right-click.
- Navigate to the “Properties” context menu → “General" tab → Security (The file originates from a different computer. Access might be denied due to safety reasons.) → Click the “Unblock” checkbox.
- Unpack the .zip file, and then install the programming station. It is important that you have administrator permissions on the installation PC.
A message about virtualization support appears during installation of the programming station. What should I do?
The programming station installation process checks whether hardware virtualization is present and active.
Smooth operation of the programming station in conjunction with the VirtualBox virtualization software requires the availability of hardware virtualization. The processor thus needs to have the VT-x or AMD-V instruction set extension. The availability of hardware virtualization depends not only on the CPU but also on the settings in the BIOS and the Windows operating system of your PC. Be sure to consider all relevant information provided by the manufacturer!
In the Task Manager, check whether >Enabled< appears next to “Virtualization” within the “Performance” tab.
The installation of the programming station software generates warnings because Hyper-V hardware virtualization is enabled. What does this mean?
Third-party virtualization applications, such as ORACLE VirtualBox or VMware Workstation, rely on the Intel VT-x or AMD-V instruction set extensions, which are available on most current processors. However, they are no longer fully available to the virtualization application if Microsoft already uses these instruction set extensions for its own functions, such as Hyper-V, WSL2 and virtualization-based security.
In order to use third-party virtualization software with hardware virtualization, you must deactivate the abovementioned functions on your PC.
Alternatively, when Hyper-V is enabled, the third-party virtualization applications can use a software interface as a replacement for the abovementioned instruction set extensions. This can result in performance losses and limited functionality that has an effect, for example, when the programming station is used in conjunction with VirtualBox. Although this combination is possible, a warning appears both when the programming station software is installed and when it is started. This combination may not be suitable for productive use of the programming station software.
HEIDENHAIN has no influence over which applications are installed on a PC or which Windows features are needed. Please check whether the use of the programming station software, including VirtualBox, is possible on the intended PC.
It is possible to use VMware Workstation as an alternative if enabling Hyper-V is unavoidable on your PC. When VMware Workstation 16 or later is used in conjunction with Windows 10 20H2, it is possible to enable Hyper-V and use VMware Workstation as a virtualizer for the programming station software with only minor performance losses. Not all versions of the programming station software are prepared for installation with VMware Workstation. VMware Workstation is not part of the installation package of the programming station software and must be installed by the user. Please note: It is not possible to install the programming station software in the VMware Workstation Player.
How can I check whether Hyper-V is enabled on my PC?
Hyper-V is enabled on my PC. What options are there for using the programming station software?
Note the system requirements along with the following information:
- HEIDENHAIN has no influence over which applications are installed on a PC or which Windows features are needed. Please check whether the use of the programming station software, including VirtualBox, is possible on the intended PC. Also check which feature uses Hyper-V and whether you can deactivate this feature along with Hyper-V.
- As an alternative to VBox, you can install VMware Workstation. If you do this, then the option of using VMware Workstation is offered during the customized installation of the programming station software. Please note: It is not possible to install the programming station software in the VMware Workstation Player!
- Test the installation of the programming station software with Hyper-V enabled to see whether it is sufficient for your needs. Although this combination is possible, a warning appears both when the programming station software is installed and when it is started. This combination may not be suitable for productive use of the programming station.
How can I install more than one programming station of the same control on my PC?
The name of the programming station to be installed is automatically assigned during installation in “Default” mode.
If you wish to install more than one programming station of the same control on a computer, select “Custom” during installation. You can now assign any name to the programming station and thus install multiple programming stations of the same control on your PC.
How can I edit a tool table on my computer?
My machining simulation mills next to the block form / component. What can I do?
With the BLANK IN WORKING SPACE soft key, the preset set in Manual operating mode can be used in the simulation.
- Switch to Test Run mode.
- Select a machining program.
- Press the BLANK IN WORKING SPACE soft key.
- Press the soft key with the machine icon.
Note: The path description to this soft key may differ on older control types. Refer to the User’s Manual of your software version as needed.
Why is the final hole of the bolt hole circle drilled twice?
What does “Angle cannot be calculated” mean?
Can I run a Siemens program on a HEIDENHAIN control?
Where can I find the signal period of my encoder?
What is the difference between EnDat02 and EnDat22?
The EnDat02 and EnDat22 order designations define different technical parameters that are important for the connection of an encoder. This includes the availability of incremental signals, the typical voltage supply range, the command set, and the maximum clock frequency. Among other things, the following table applies:
Incremental signal | Voltage supply range | Command set | Max. clock frequency | |
EnDat02 | With 1 VPP incremental signal | 3.6 V to 5.25 V or 3.6 V to 14 V | Command set 2.2 | ≤ 2 MHz or |
EnDat22 | Without incremental signal | 3.6 V to 5.25 V or 3.6 V to 14 V | Command set 2.2 | ≤ 8 MHz or 16 MHz |
Please refer to the interface brochure with its additional information and exceptions noted in the technical data.
For more information about EnDat, please refer to www.endat.de/de_EN/.
Can I send my AMO device to HEIDENHAIN for repair?
Where can I order replacement devices and replacement parts from AMO?
Contact the HEIDENHAIN Service department:
+49 8669 31-3121, service.order@heidenhain.de
Or contact your nearest representative:
Where can I find mounting instructions and CAD data for AMO encoders?
Mounting instructions:
For more information, visit:
https://www.amo-gmbh.com/en/downloads/mounting-instructions/
CAD data:
For more information, visit:
https://www.amo-gmbh.com/en/downloads/cad-files/
What do I need to send in for repairs with MHS?
Which testing device do I need for AMO devices?
Where can I get a calibration chart from AMO?
Please send your request, including the relevant ID and serial number, to 3104@heidenhain.de.
What should I do if, during an update of the EIB 7xx firmware, this notification appears: "'tftp' is not recognized as an internal or external command, operable program or batch file."?
Please check whether the TFTP client has been activated:
- Press the Windows key + “R”.
- Enter “appwiz.cpl” and press enter.
- The “Programs and features” function appears.
- Click “Activate or deactivate Windows features” on the left side.
- A window with the available Windows features appears. Select the check mark for “TFTP client” if it has not already been selected.
- The TFTP Windows client is installed and is immediately available without restarting the system.
During the firmware update of my EIB 7xx, I get a “Connect request failed” message. What can I do?
How can I perform a firmware update on my EIB 7xx?
The firmware of the EIB 7xx can be updated as follows:
- Download the current firmware.
- Save the update file to “C:\temp\EIB\update_633281-xx.flash”.
- Press the Windows key + “R”.
- Enter “cmd” and press enter.
- Enter “tftp –i 192.168.1.2 put C:\temp\EIB\update_633281-xx.flash tmp\update.flash” and press enter (adjust IP address as needed).
- When the file has been successfully transferred, the status LED of the EIB 7xx goes out. The voltage supply must not be switched off at this time, and no TCP commands may be sent to the EIB 7xx.
- When the status LED is active again, the EIB 7xx can be restarted.
For more information about performing a firmware update, refer to the Firmware Update section of the User’s Manual. The current User’s Manual can be found in the "User documentation" section of the download area. Unter "Filebase: documentation", Select the following fields in the dropdown menu:
- Category: Evaluation units
- Product family & software solutions: EIB
How can I check the current firmware of my EIB 7xx?
Where can I find the most current firmware for my EIB 7xx?
I cannot reach my EIB 7xx with the standard IP / I cannot remember my EIB 7xx’s IP. What can I do?
If the EIB 7xx cannot be reached, then the default network settings of the EIB 7xx can be loaded by means of a reset. To do this, press and hold the reset button on the back of the device for more than ten seconds.
For more information, please refer to the section "Reset modes supported by the product" in the Operating Instructions. To do so, select the following fields in the dropdown menu under Filebase: documentation.
- Category: Evaluation electronics
- Product family & software solutions: EIB
In the ATS software, the “Connect the encoder” menu is not displayed.
Do I need a product key in the ATS software for my PWM 20/PWM 21?